Author:
madshen Add Time:2015-11-18 09:01:40
1, part of the power supply branch
380V 50HZ three-phase five wire power supply separately, as shown in the table below.
The details of the power supply of galvanizing line |
Electrical classification | The installed power KW | The nature of the load | Explain |
|
C typeresistancewelding machine | Four hundred | inductive load | Three-phase unbalance |
|
Drying furnace | Three hundred | Resistive load |
|
|
Withdrawal and straightening unit | Two hundred and thirty-five | DC motor |
|
|
Zinc pot | Six hundred | Balance compensation cabinet with a cabinet |
|
|
transmission | Six hundred and twenty-five | Variable frequency motor |
|
|
Technology | One thousand | Fan and water pump |
|
|
Protective gas | Five hundred | The main resistance load |
|
|
Light machine | Two hundred and twenty | DC motor |
|
|
Electrolytic degreasing | Two hundred and twenty | Bidirectional DC power supply |
|
|
Annealing furnace | Five thousand and eight hundred | Electric radiant tube |
|
|
The total installed power 10000KW .
Two control The general description of the structure2.1 the whole line control Technical performanceA general control system of production line.The device has a relatively independent independent control The system, with separate debugging section.All of the equipment control The system is connected by bus and control system.equipment control Using PLC control The equipment. control Device and driver with high speed field bus connection.Motor adopts photoelectric encoder as the speed detection.A single device with emergency stop, manual / automatic, single / line.Device with overload, fault detection, diagnosis and protection function.main control Parts selection of international famous brand products.control The system has high openness, interoperability, interchangeability, integration, high reliability and maintainability.2.2 production line control system configurationIn order to make the production line control Coordinated whole control The system uses two PLC CPU control PLC, SIEMENS SIMATIC S7-300 CPU, CPU and PROFIBUS touch screen through the network connection. control Using the Madshen system Mr De Sheng Brand MDSC308E series switch input / output signal (DI/DO) about 720 points, using MDSC306E series analog input / output signal (AI/AO) 9, through field bus connects the I/O module. The transmission system of the rolling mechanism, a tensioning mechanism and storage mechanism, motor bottom roller mechanism adopts the vector inverter control And through PROFIBUS-DP, with PLC communication . Ordinary AC motor drive part and the part of the process is divided into two different starting modes according to the size of the motor light load equipment (power is below 37KW) with direct starting mode (full voltage starting), heavy load starting of the motor (more than 37KW) by "star delta starting.The operating table and the touch screen is through the PROFIBUS bus and PLC communication It can, for each load running state of the corresponding module control And the adjustment of operation parameters, and can display the running state of the load, due to its distance control The equipment can be carried out close, very convenient controlAnd monitor.The operation panel can receive operation command and parameter setting, the command sent to the PLC CPU, but also can receive PLC signal, display the current state of equipment and various system parameters. The I/O module is responsible for the acquisition of line detection and signal. control Production line actuator.All operation module accept external touch screen control Signal: including operating parameters, start and stop command, solenoid valve action command; at the same time, the running status of devices through PLC transmitted to the touch screen, touch screen display and monitor, and sends out alarm signal. The touch screen data through the PROFIBUS network communication , to record production data, real-time display of parameters to adjust the running state of the system or equipment. PLC touch screen control And signal control The amount of each devicecontrol To ensure the operation of the production line.In addition to the touch screen and the operation panel, in uncoiling, rolling, welding, straightening, oiling and other necessary position is also provided with a manual operation panel, the operation is convenient. In line with many emergency stop button, set the appropriate prompt and alarm device, easy to deal with emergency accidents, ensure the safety of equipment and operating personnel.Detection and distribution line device control Device and software function of tight to ensure the safety of equipment across the board. The detection device is divided into correction, in the detection, photoelectric detection, position detection, detection of weld length, etc..The galvanizing line is a advanced manufacturing process and the level of automation engineering, the control The system mainly includes the following operation table:A uncoiling operation tableThe operation of B process in TaiwanC finishing operation tableD straightening benchE coiling operation tableThe system will be based on production control The process requirements, according to the design specification of CIMS, the automatic design of galvanizing line control Meet the system, automatic line control Requirements and management.
Two point three control Module structure diagram
control System configuration diagram 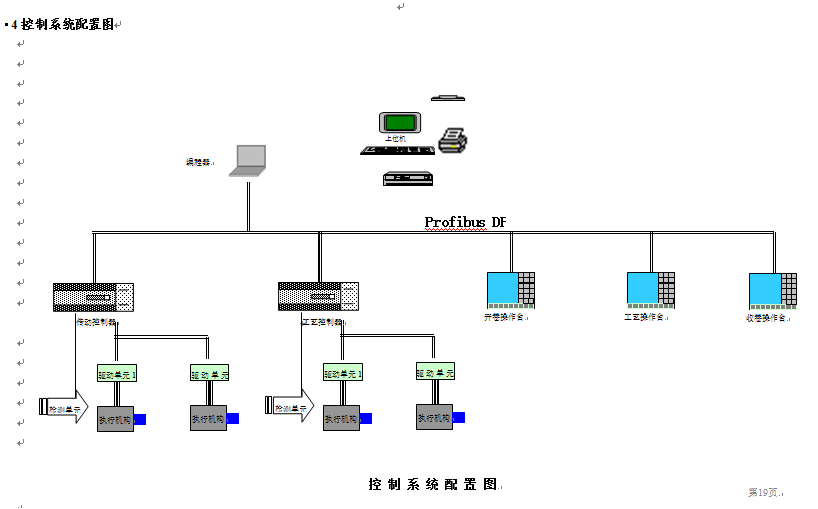
Tags:
Continuous hot galvanizing production line electrical automation system
Browse: